Global steel production has reached close to 2 billion tonnes per year, with China accounting for more than 50% of this total. Steel production is a significant source of emissions, responsible for about 7-9% of global carbon dioxide emissions.
This article highlights a number of technical solutions for reducing the level of carbon dioxide emissions during steel production and examines international patent application trends over the last 20 years. The results indicate that United States and European applicants dominate international patent applications in the field, with, perhaps surprisingly, relatively few international applications from Asian applicants. Further, even in recent years, the number of applications is relatively low, suggesting a lack of innovation in the sector.
The carbon intensity of steel production varies significantly depending on the production method. The blast furnace-basic oxygen furnace (BF-BOF) method, which is the dominant production method, has a carbon intensity of around 1.8-2.2 tonnes of carbon dioxide per tonne of steel. Electric arc furnace (EAF) steelmaking, which uses scrap steel as a raw material, has a carbon intensity of around 0.5-1.0 tonnes of carbon dioxide per tonne of steel.
Reducing emissions from this sector is challenging but will be critical to meet global climate goals. While there have been some efforts to reduce emissions, much more needs to be done to transition to more sustainable steel production methods.
Technology developments
Several key trends have emerged in recent years including:
- Increased use of scrap steel as a raw material: This approach, known as electric arc furnace (EAF) steelmaking, uses electricity (potentially from renewable sources) to melt and reform scrap steel, rather than relying on coal and iron ore. EAF steelmaking produces significantly lower carbon emissions than traditional steelmaking methods.
- Hydrogen-based steelmaking: This is another promising trend in sustainable steel manufacturing where hydrogen is used as a reducing agent in the steelmaking process. This approach, known as direct reduction, involves using hydrogen to convert iron ore into sponge iron, which can then be melted and formed into steel. Hydrogen-based steelmaking produces no carbon emissions, potentially making it a highly sustainable option.
- Direct Reduced Iron (DRI) with natural gas: This method produces lower CO2 emissions compared to coal-based reduction.
- Electrolysis of iron ore: This may potentially be powered by renewable electricity.
- Carbon capture and storage: Carbon capture and storage (CCS) technology is becoming increasingly important in sustainable steel manufacturing. CCS involves capturing carbon emissions from the steelmaking process and storing them underground, rather than releasing them into the atmosphere. While CCS technology is still in the early stages of development, it has the potential to significantly reduce carbon emissions from steel manufacturing.
- Energy efficiency: Energy efficiency is a key focus in sustainable steel manufacturing, with manufacturers seeking to reduce their energy consumption and associated carbon emissions. This can be achieved through a range of measures, such as optimizing production processes, using more energy-efficient equipment, and recovering waste heat.
- Circular economy: This approach involves designing steel products to be more durable, reusable, and recyclable, and creating closed-loop systems for the reuse and recycling of steel.
Patent trends
International patent application publications (PCT publications) are a useful proxy for relatively significant developments in a technical field of endeavour. We therefore searched for PCT publications published between 2004 and 2024 in the field of sustainable steel manufacture.
Figure 1 illustrates the number of PCT publications in sustainable steel manufacture from 2004 to 2024.
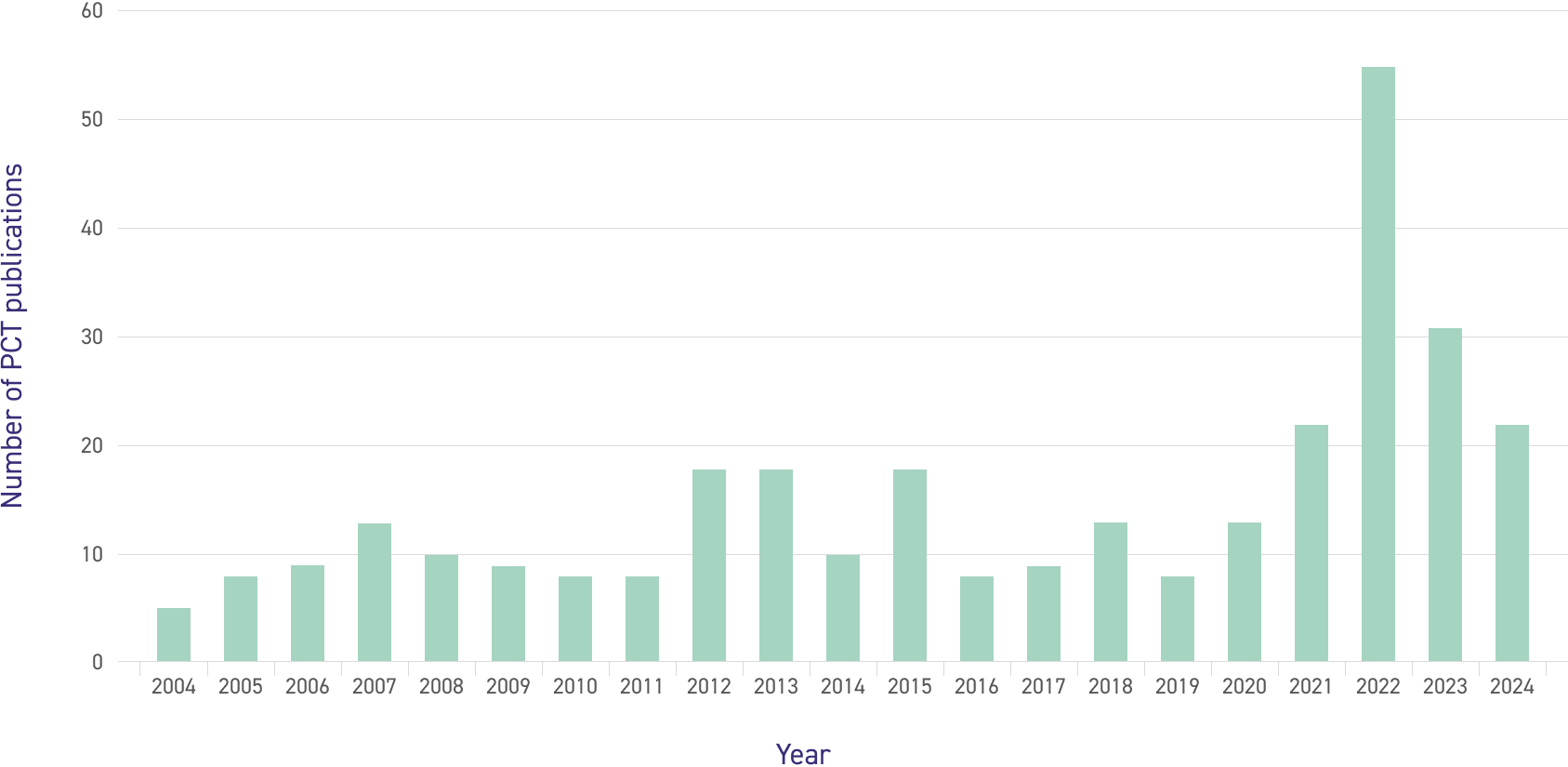
The results indicate that the number of PCT publications per year from 2004 to 2020 has remained relatively static. However, since 2020 there has been a reasonable increase in PCT publications in this space, likely due to the increased efforts to make steel manufacture more sustainable. Despite this, even in recent years the number of publications is relatively small compared to other clean technology sectors, reinforcing the notion that greater efforts in sustainable steel innovation are required.
Figure 2 shows the top geographical areas that patent applicants reside.
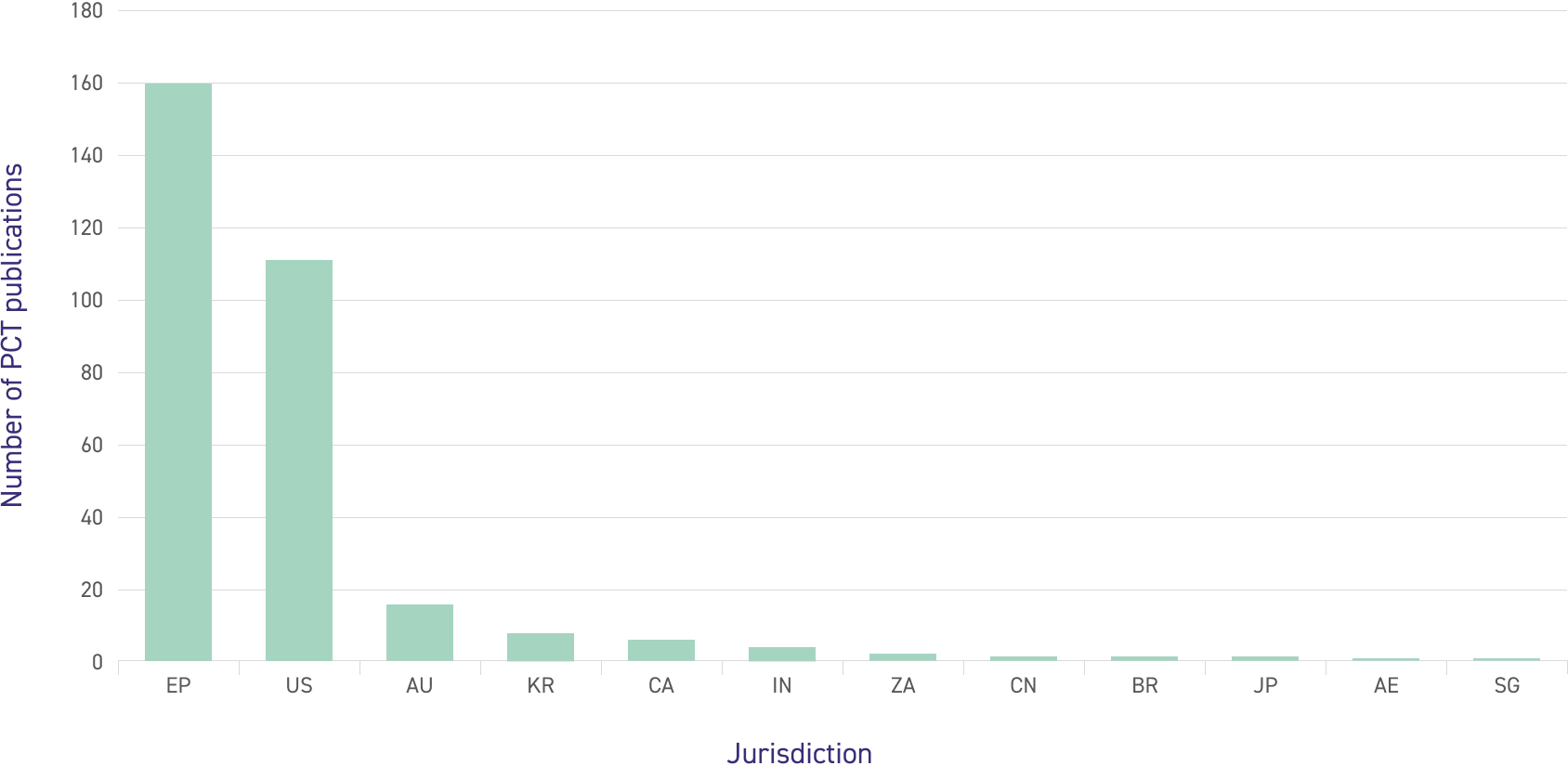
This graph illustrates a very similar trend to one we recently found when conducting a similar analysis for PCT publications in the field of sustainable cement. US and European applicants dominate publication numbers, and very few results were returned from Asian applicants. As with sustainable cement, this is perhaps surprising given China alone is responsible for 50% of global steel production. Australian applicants also perform reasonably well in this metric, with both corporate and university-based applicants being returned in our search, hinting at a competitive local space.
Figure 3 illustrates the top applicants in sustainable steel manufacturing.
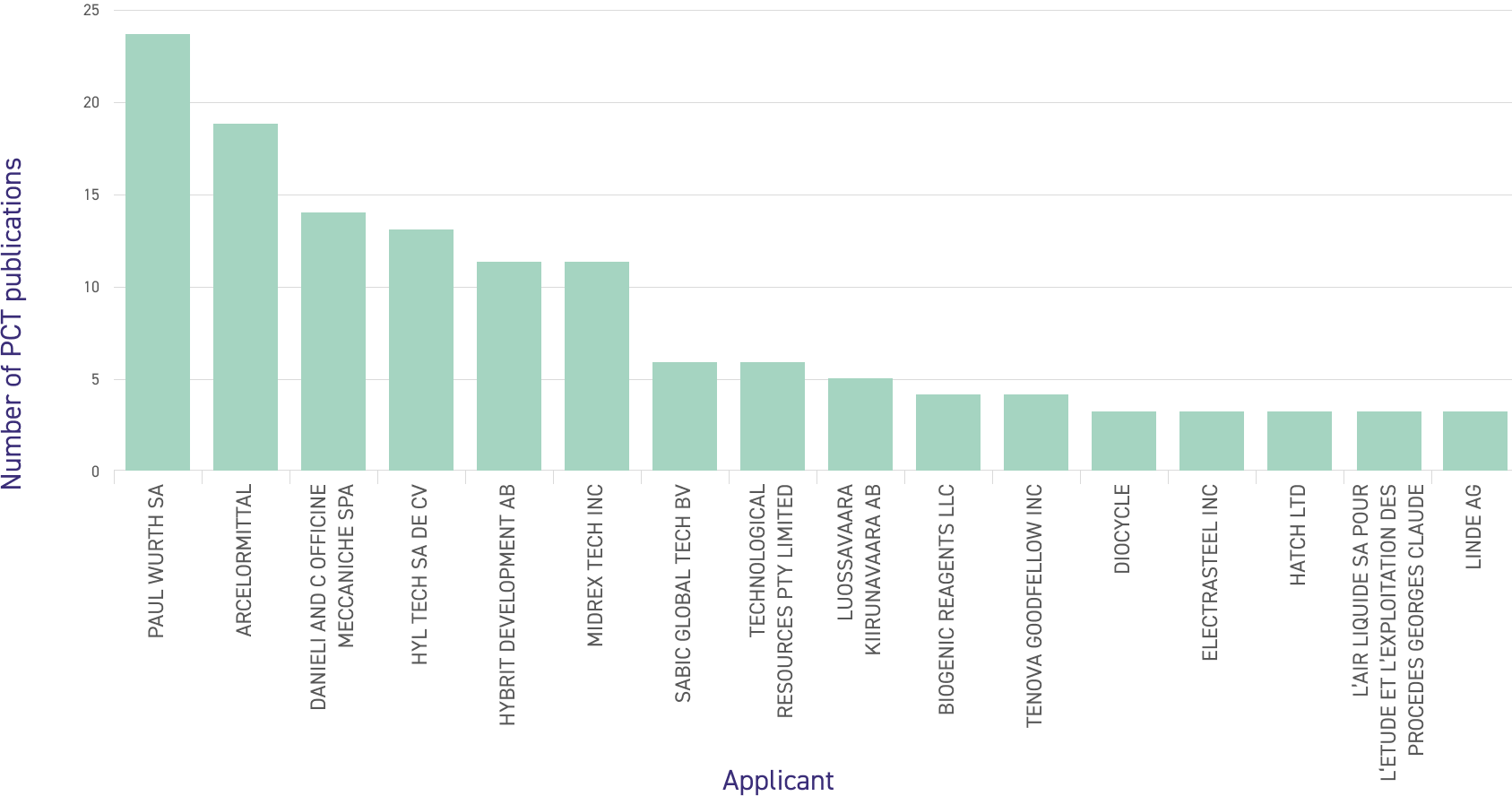
US and European applicants make up the majority of the top patent application filers, which is unsurprising given the geographical areas shown in Figure 2. Luxembourg based Paul Wurth SA and ArcelorMittal are unsurprisingly two of the biggest filers here. Paul Wurth SA is a major equipment supplier to the steel industry and ArcelorMittal are the world’s largest producers of steel outside of China. Australian activity is modest in comparison to Europe and the US, with several patent applications recently filed by Technological Resources Pty Ltd (Rio Tinto).
Further remarks
As was the case for sustainable cement, our patent searching shows that there are a relatively low number of international patent applications directed to sustainable steel manufacture owned by Asian applicants, in contrast to what is observed for most technologies. This is particularly true for China as they are by far the world’s largest steel producer.
China produced around 1 billion tonnes of steel in 2023, largely through the blast furnace-basic oxygen furnace process, and most of it remained in the country for domestic use. However, over the last few years, the downturn in the Chinese domestic construction market has seen steel exports increase to 90 million tonnes in 2023, with most of these exports going to developing countries. Further, Chinese steel companies are increasing overseas investment in building steel plants, mostly in the ASEAN region. Despite these relatively recent developments, it would appear that Chinese steel companies have presently little interest in seeking patent protection for sustainable steel innovations internationally.
FPA Patent Attorneys has a coordinated CleanTech team comprising patent professionals with chemical and engineering expertise. Please contact us to discuss your sustainable steel technologies.